"APRENDER PROGRAMAR PLCs"
Un PLC (Programmer Logic Controller) es un controlador lógico programable diseñado para ejecutar procesos de automatización en la industria. Se compone de un sistema operativo (firmware) y de un entorno de programación que puede soportar uno u varios lenguajes. Estos dispositivos se vienen empleando para la automatización de procesos desde 1970. Desde entonces su tecnología ha ido mejorando y hoy en día ofrecen grandes prestaciones para la industria. En este artículo te explicaremos las claves de la programación en PLC.
A diferencia de un computador tradicional, los PLC o autómatas programables, no tienen teclado, ni ratón, ni disco duro, ni monitor. No obstante, sigue siendo un ordenador, con su hardware y con su software. La diferencia principal que encontramos entre un PLC y un PC normal es que el PLC recibe señales a través de diversos canales de entrada conectados a sensores instalados en la máquina o proceso que controlan. De la misma manera, dispone de unos canales de salida para transmitir las órdenes a las máquinas y activar procesos automáticos. Un PLC permite controlar y monitorizar en tiempo real los diversos procesos industriales, presentándolas en un HMI (interfaz hombre-máquina) o en redes de control superior. Podemos encontrar sistemas PLC en muchos ámbitos diferentes: control de presas, subestaciones, distribución de gas, petroquímica, cadenas de producción, etc...
PROGRAMACIÓN EN PLC
Programar un PLC implica generar un conjunto de instrucciones y de órdenes que provocarán la ejecución de una tarea determinada. Podemos decir que un programa es una respuesta predeterminada a todas las combinaciones posibles de estados de la información que recibe. La programación en PLC se compone de diversas fases:
1 - Definición y análisis del problema: En primer lugar debemos identificar cuál es la necesidad que queremos resolver a través de la controladora programable. ¿Qué resultados nos debe proporcionar el sistema? ¿Qué datos o información nos hacen falta para poder determinar la respuesta de la máquina?
2 - Definición de la arquitectura del automatismo: Definiremos el hardware de la controladora. Una vez que sepamos cuál es la información o los procesos que necesitamos monitorizar, configuraremos las entradas de la controladora para que pueda recibir los datos que se recogen a través de los sensores. Se definen también las salidas a través de las cuáles se activarán procesos, y factores como la redundancia o el diagnóstico.
3 - Diseño de los algoritmos: Un algoritmo consiste en una secuencia de los pasos requeridos para ejecutar una tarea. Así, se diseñara el método para la toma de decisiones.
4 - Programación de código: Con todos los procesos definidos, pasaremos a redactar las órdenes que nos permitirán comunicarnos con la máquina. Para ello se emplean los lenguajes de programación.
5 - Depuración, test y verificación del programa: La última fase implica una serie de tareas orientadas a comprobar el correcto funcionamiento del programa. Se detectan posibles errores en la comunicación y se hacen las correcciones oportunas para garantizar una óptima ejecución del automatismo programado.
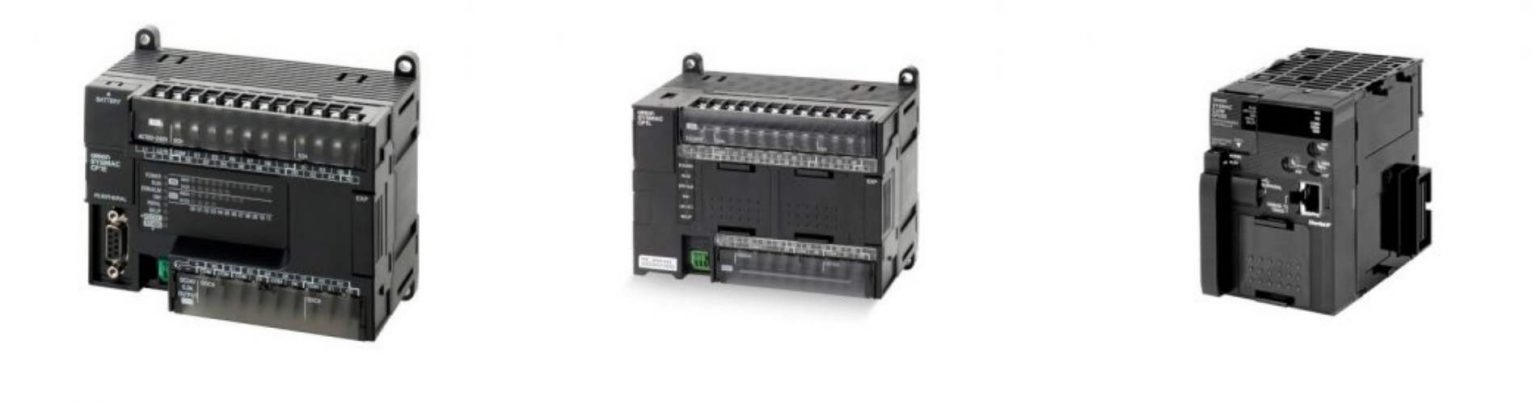
LENGUAJES DE PROGRAMACIÓN EN PLC
1 - IL (Instruction List): Es un lenguaje de texto y es el lenguaje de programación más antiguo. En realidad, es la base del resto de lenguajes y se empleaba cuando las computadoras no tenían capacidad gráfica. El IL es un lenguaje de bajo nivel y recuerda al lenguaje ensamblador. En este lenguaje todos los programas pueden ser traducidos a una lista de instrucciones. El control del programa se consigue a través de "saltos" y de llamadas a funciones.
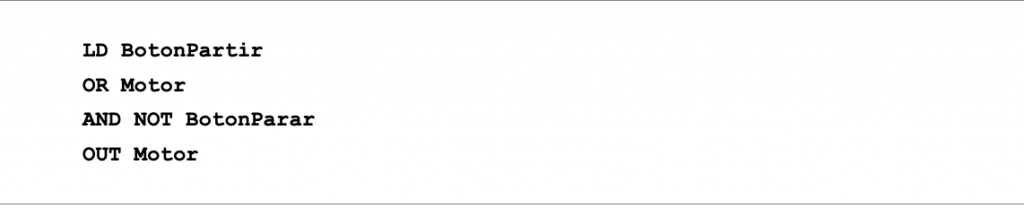
2 - LD (Ladder): Es un lenguaje gráfico y es la evolución del lenguaje IL. El lenguaje Ladder se conoce también como Diagrama de Escalera, ya que su estructura recuerda a la de una escalera: se compone de dos niveles verticales (alimentación) y de dos horizontales. Las instrucciones se colocan en el lado izquierdo y las salidas en el lado derecho. El procesador del PLC interpretará los lados de abajo arriba y de izquierda a derecha.
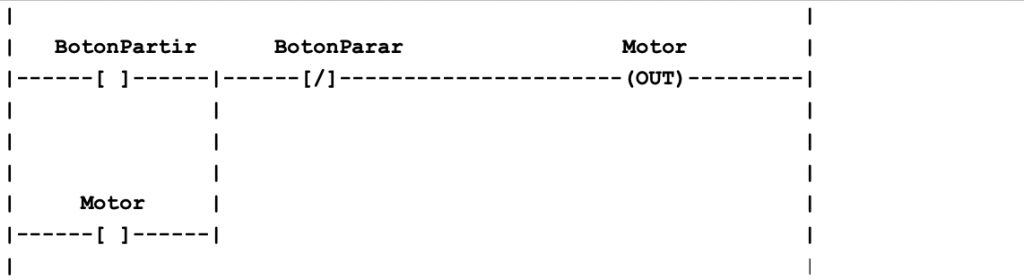
3 - FBD (Function Block Diagram): Es un lenguaje gráfico que define la función entre las variables de entrada y las de salida. En este lenguaje se utilizan bloques de símbolo lógico.
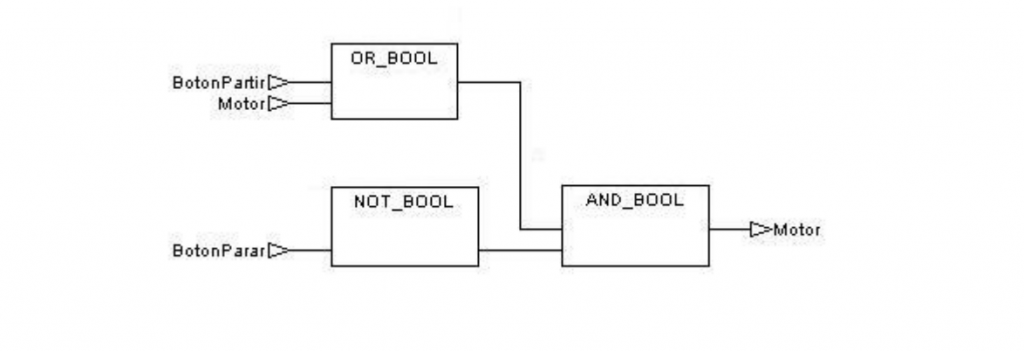
4 - ST (Structured Text): Es un lenguaje gráfico que define la función entre las variables de entrada y las de salida. Recuerda al lenguaje de programación C y al Pascal. Se compone de una serie de instrucciones que se pueden ejecutar de manera condicionada.
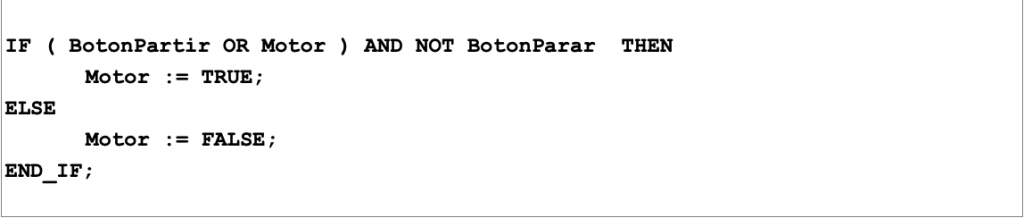
Es importante saber que la funcionalidad es un aspecto a medida en el desarrollo del PLC. Pues el proveedor desarrolla las funciones según las necesidades de control, registro, monitoreo... del proyecto que se está desarrollando.
Este equipo como un ordenador, donde las partes principales son la CPU, un módulo de memorias y de entradas/salidas, la fuente de alimentación y la unidad de programación. Para que funcione, entonces, es necesario que se realice una programación previa a la función que va a realizar.Para realizar esta programación se necesita un software específico adaptado a la marca y al lenguaje de programación que se va a desarrollar.
¿Cómo nacen los dispositivos PLC?
Con el desarrollo de internet y de las tecnologías electrónicas se buscó la forma de reemplazar los sistemas de control basados en circuitos eléctricos de lógica combinacional, con relés e interruptores.
A finales de la década de los 60 aparecieron los primeros tipos de autómatas programables, con características muy sencillas y una vida útil muy larga.
Se buscaba conseguir la automatización industrial, donde el uso de dispositivos electrónicos aliviara la carga de tareas repetitivas en las fábricas. Así se produjo una evolución laboral donde, el profesional dejaba de realizar el trabajo y comenzaba a vigilar que la máquina funcionara de forma correcta.
En 1982 se vendió el primer PLC comercializado de forma estandarizada por más de un millón de dólares. Sin embargo, ahora este tipo de tecnología está disponible desde los 49 dólares (43€).
Cuando aún la historia estaba comprendiendo qué es un PLC, se incorporaron los microprocesadores a su composición. Se crearon, así, PLCs con capacidad de comunicarse entre ellos y controlar los procesadores de forma telemática. Se implementaron, además, mejoras tecnológicas que mejoraran los datos obtenidos.
En los años 80 se estandarizó el protocolo de programación y comunicaciones, realizando mejoras en el sistema de programación para que se pudiera realizar, en lugar de con terminales de programación, con ordenadores personales. Además, se implementaron otras mejoras de diseño que mejoraron sus prestaciones.
A partir de los años 90, y hasta ahora, se modernizaron las características físicas de los dispositivos y los módulos de programación, abriendo las posibilidades de programación, control y los canales de comunicación.
¿Qué tipos de PLC existen?
Como hemos visto en la evolución de los PLCs, las modificaciones y mejoras que se han ido realizando han derivado en diferentes tipos de PLC que se pueden agrupar en cuatro categorías principales.
Tipo compacto
¿Quieres saber qué es un PLC compacto? Es aquel que se ajusta a las especificaciones genéricas de los PLCs: tiene incorporada la fuente de alimentación, la CPU y los diferentes módulos.
Existen PLCs compactos en tamaño nano, que cuentan con un tamaño súper reducido, aunque el funcionamiento básico del PLC está más limitado por sus características. Todos nuestros equipos disponen de entradas para acoplar nuestros sensores de temperatura, presión, humedad, etc. Con los que podra realizar un control de precisión de su maquinaria y equipos.
Tipo modular
Esta clase de PLC se caracteriza por estar compuesto por módulos ampliables, lo que le aporta características más potentes que el modelo compacto. Trabaja con programas más complejos, tiene mayor capacidad de memoria y operatividad.
Montaje en rack
Cuando sabes qué es un PLC modular es más fácil comprender el montaje en rack. Es prácticamente igual, pero existen diferencias en el rack donde se colocan los módulos del PLC.
En el caso del montaje en rack se permite el intercambio de información entre los diferentes módulos, esto permite una velocidad mayor de transmisión de la información y, por tanto, optimiza el funcionamiento del PLC.
PLC con HMI incorporado
El HMI (Human Machine Interface) es un dispositivo programable, una interfaz gráfica, que combinado con el PLC permite optimizar la experiencia de programación y uso de la máquina. Reduce el cableado de los elementos del PLC y los muestra en una pantalla gráfica según se programe.
¿Qué utilidad puedo darle a esta tecnologia?
Esta tecnología de implementación sencilla y ejecución rápida, nos permite automatizar los procesos de nuestro proyecto con un bajo mantenimiento e instalación personalizada.
Para terminar de comprender qué es y cómo funcionan esto equipos, vamos a poner el ejemplo de un túnel de lavado automático:
Se programará para que, cada 500 metros, recoja las señales de diferentes sensores de temperatura, presión, presencia de vehículos, niveles de óxido y dióxido de carbono, y el nivel de agua del depósito.
En función de los sensores, se activarán los dispositivos de entrada y salida: semáforo, avisos luminosos, ventiladores y bomba de agua. Además, al tener acceso remoto, los operadores pueden acceder a la interfaz de la máquina y visualizar el estado del proceso, además de modificarlo en caso necesario.
En definitiva, se establecerán unos niveles de seguridad en presencia de los gases tóxicos, de la velocidad del vehículo, etcétera, y el PLC comprobará que los datos se encuentran dentro de ese parámetro y, en caso de que no sea así, activará las medidas de seguridad programadas.
Ahora que conoces perfectamente qué es un PLC, te informamos de que en SRC contamos con una línea de desarrollo de estos productos. Nuestros ingenieros, además, son los encargados del desarrollo de los sistemas de automatización para acoplar nuestros sensores de temperatura, presión, humedad, etc. Con los que podra realizar un control de precisión de su maquinaria y equipos.
Un puente PCI es la conexión del hardware entre dos buses diferentes. El puente puede ser PCI a PCI, PCI a ISA u otro tipo de bus. Los estándares de estos están limitados por las características eléctricas. Agregar dispositivos llamados puentes permite que los buses se expandan. Un puente PCI permite la expansión de el bus PCI al agregar más buses al sistema
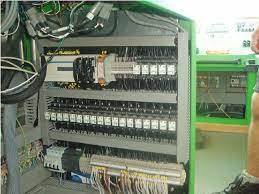
Los controladores de los dispositivos PCI son programas diseñados para operar estos dispositivos ubicados en el bus PCI. Cada tarjeta o dispositivo específico en el bus PCI necesita su propio software controlador. Las tarjetas de expansión de terceras partes que operan con sus propios controladores de dispositivo le permiten a los fabricantes construir tarjetas de expansión sin conocer la configuración específica de una tarjeta madre. El fabricante desarrolla el dispositivo para conformarse al estándar del PCI y codifica una unidad de dispositivo para ejecutarla. El sistema operativo integra el dispositivo al sistema.
Los servidores en rack están diseñados para ser instalados en los bastidores de ordenador o servidor. Estas cajas varían en tamaño, desde 23 pulgadas (58 cm) de ancho por 36 pulgadas (91 cm) de profundidad por 36 pulgadas de altura hasta llegar a 24 pulgadas (60 cm) de ancho por 36 pulgadas de profundidad por 84 pulgadas (2,1 m) de alto. La altura del rack del servidor se mide en unidades llamadas "U". Una U es de aproximadamente 1,75 pulgadas (4 cm) de altura.
Un servidor blade es un chasis o carcasa que alberga múltiples servidores físicos o cuchillas dentro de él. Todo el sistema a menudo está montado en bastidor. Los servidores blade varían en tamaño, pero normalmente son entre 4 y 8 Us de tamaño. El chasis es rectangular, al igual que los servidores de bastidor, pero los servidores individuales alojados en ella se han instalado de manera que sean perpendiculares a la carcasa de la cuchilla. Dentro de una cantidad 8U de espacio, un servidor blade físico puede albergar de 16 a 32 o más hojas.Los servidores en rack varían en precio, dependiendo de la cantidad y la calidad de los componentes de hardware en el propio servidor. Los servidores de nivel básico comienzan en US$700 y se pueden escalar hasta llegar a US$6.000 por servidor. Una vez más, esto es para un único servidor independiente.
Los servidores blade varían en precio también, pero con el entendimiento de que son más caras las hojas para añadir en el interior del chasis. Los gabinetes blade comienzan alrededor de US$2.000 y pueden costar tanto como US$15.000 o más. Esto es sólo para el chasis y no para cada hoja individual. Una hoja puede ser tan barata como US$500, pero se extenderá hasta el final a US$2.000 cada una.
Consideraciones
Elige el tipo de servidor dependiendo de tus necesidades. Si tu empresa necesita o necesitará un gran número de servidores, y considera la tecnología de servidores blade. Además de ser más eficientes en espacio, tienden a ser más eficientes que tener un número equivalente de servidores de bastidor independientes alimentados de forma individual. Si estás en busca de las opciones para una empresa más pequeña, considera un servidor en rack. De la comparación uno a uno, el chasis de servidor blade y el servidor de una sola hoja es significativamente más caro que un servidor de rack. Un servidor blade no llega a ser rentable hasta que haya un número importante de servidores de este tipo alojados en el recinto. Además, si el chasis de servidor blade deja de funcionar, esto afectará a todas las hojas que se hallan en el interior .
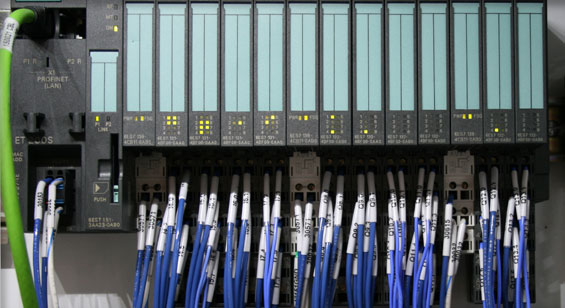
El primer componente fundamental para la implementación exitosa de ERP es un software modular. El software modular realiza tareas completamente diferentes para cada departamento específico dentro de un negocio. Un sistema ERP podría proporcionar un único conjunto de software que funciona tanto para los departamentos de contabilidad como de nóminas, aunque el software típicamente abarca todos los departamentos, de acuerdo con ERPFans.com. Esto es clave para el éxito de un ERP; alternativamente, cada departamento debe ejecutar software completamente diferente e incompatible. Cuando una solución de software maneja todo, lo hace infinitamente más fácil de planificar, presupuestar y de otra manera manejar el negocio.
Base de datos universal
El software ERP debe estar relacionado con una base de datos universal. Sin una sola base de datos, el software modular tendría que almacenar y ser accedido a través de diferentes sistemas, lo que requiere más tiempo y esfuerzo. Lo que facilita la comunicación y el intercambio de información entre los distintos departamentos, que ayuda a racionalizar las funciones del negocio y proporciona mayor eficiencia a través de módulos de software individuales capaces de actuar como un todo.
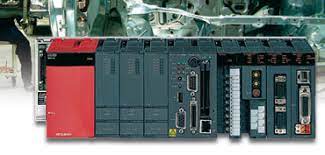
Usabilidad
La implementación de un sistema ERP por lo general requiere una gran cantidad de cambios dentro de la empresa. Más que un simple intercambio de equipos o la instalación de un nuevo software, un sistema ERP exitoso está diseñado específicamente para satisfacer las necesidades de una empresa individual. NetworkDictionary.com advierte que un sistema ERP completo podría tomar años integrarse con éxito en una gran empresa con muchos departamentos y ubicaciones. Un sistema ERP tiene que ser adaptado específicamente de esta manera con el fin de lograr una plena compatibilidad. Incluso un módulo de software incompatible puede hacer caer todo el sistema.
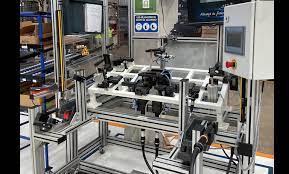
Un PLC (Programmer Logic Controller) es un controlador lógico programable diseñado para ejecutar procesos de automatización en la industria. Se compone de un sistema operativo (firmware) y de un entorno de programación que puede soportar uno u varios lenguajes .Este computador autómata es capaz de recibir diferentes señales de entrada que secuencialmente realizarán una acción específica (Salidas). Su origen se remonta a los años 60's como una alternativa a los antiguos sistemas de relés, en un inicio fueron programados con el lenguaje de listado de instrucciones, posteriormente llegaría un lenguaje de interfaz gráfica llamado Ladder, también conocido como lenguaje escalera y que hoy en día es el más utilizado.
Aplicaciones
Es momento también de hablar de cuáles son sus principales aplicaciones. De antemano sabemos que gracias a su distinguida resistencia su uso se ha diversificado en la industria. Indudablemente los encontramos controlando procesos secuenciales, pero también en aquellos ligeramente cambiantes, imprescindible en espacios reducidos, en maquinaria de procesos variables y en chequeo de programación centralizada.
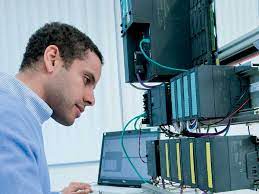
La capacitación en el ámbito industrial siempre ha sido vital. Su importancia radica en asegurar procesos de producción, así como la seguridad de sus operarios. En la era de la automatización, el personal de plantas industriales requiere de un entrenamiento especializado. La capacitación, vista de esta forma, es una inversión a largo plazo para las empresas.
El controlador Lógico Programable, también conocido como PLC, es uno de los instrumentos más utilizados en la industria. Su correcta operación es esencial y, por esta razón, algunas empresas desarrollan programas de capacitación para modelos específicos.
La programación PLC Siemens es uno de los cursos de capacitación más buscados para operarios. En específico, para la operación de los SIMATIC y SIMATIC S7-300. Los cursos de capacitación no solo son buena inversión para las empresas, sino también para los profesionales. En un mercado cada día más competido, capacitarse en programación PLC Siemens puede garantizar un mejor empleo.

Cada vez más se van incorporando a la vivienda todo tipo de automatismos que aumentan el confort y la seguridad de sus instalaciones, así como el ahorro energético. Persianas eléctricas, reguladores de intensidad de luz, toldos que se recogen de forma automática para prevenir roturas por el viento, etc .Estos aparatos eléctricos significan una revolución en la automatización industrial, ya que no sólo reflejan un verdadero ahorro en operación, si no que simplifican los procedimientos en los que antes se encontraba un equipo completo de recurso humano.
Así, son un elemento clave para la modernización de las empresas, debido a que han ido sustituyendo controles basados en circuitos eléctricos, relés, interruptores y otros componentes.
Otro de los factores por los cuáles los PLC han tenido tanto éxito como componentes en la industria es que, debido a que los lenguajes de programación han tenido grandes avances, cada vez es más sencilla la formación de técnicos que puedan desarrollar aplicaciones específicas para la industria, lo que representa un ahorro al momento de la contratación de estos servicios.
Un punto más de la importancia de estos dispositivos para la industria moderna es la conexión a internet, debido a esta conexión, se puede realizar un monitoreo constante del funcionamiento desde cualquier computadora, tanto dentro de la fábrica como fuera de ella.
Mejor control de tus procesos con un PLC
El PLC trabaja de la mano con los sistemas de combustión, ejecutando comandos programados y controlando las variables de procesos.
Anteriormente requerían ser programados por un especialista en IT para enlazarse con los sistemas operativos, pero actualmente cuentan con rutinas ya pre-programadas, tarjetas y plataformas que facilitan la interpretación de la información para el personal técnico.Controlador Lógico Programable: PLC o Controlador Lógico Programable son dispositivos electrónicos muy usados en Automatización Industrial. Un PLC controla la lógica de funcionamiento de maquinas, plantas y procesos industriales, procesan y reciben señales digitales y analógicas y pueden aplicar estrategias de control. Programmable Logic Controller o Controlador lógico programable.
- Fácil de usar y potentes conjuntos de instrucciones
- Driver de comunicación abierto
- Entorno operativo de fácil uso
- Tecnología del núcleo SoC
- Potentes funciones de comunicación
CARACTERISTICAS DE LOS AUTÓMATAS / PLC
Entradas / Salidas
Por lo general, RS-232 9-pines, pero opcionalmente EIA-485 o Ethernet son también muy frecuentes. Modbus, BACnet se suele incluir como uno de los protocolos de comunicación. Otras opciones incluyen buses de campo diferentes, tales como DeviceNet o Profibus.La mayoría de los PLC modernos pueden comunicarse a través de una red a otro sistema, como un equipo que ejecuta un sistema SCADA (control supervisor y adquisición de datos) del sistema o navegador web.Comunicaciones Peer-to-peer (P2P) son empeladas igualemente. Estas vías de comunicación son de uso frecuente para los paneles de operador, tales como teclados o estaciones de trabajo tipo PC
Programación PLC
Time Scan o Tiempo de Ciclo